3D Printing in Car Manufacturing: A Game Changer?
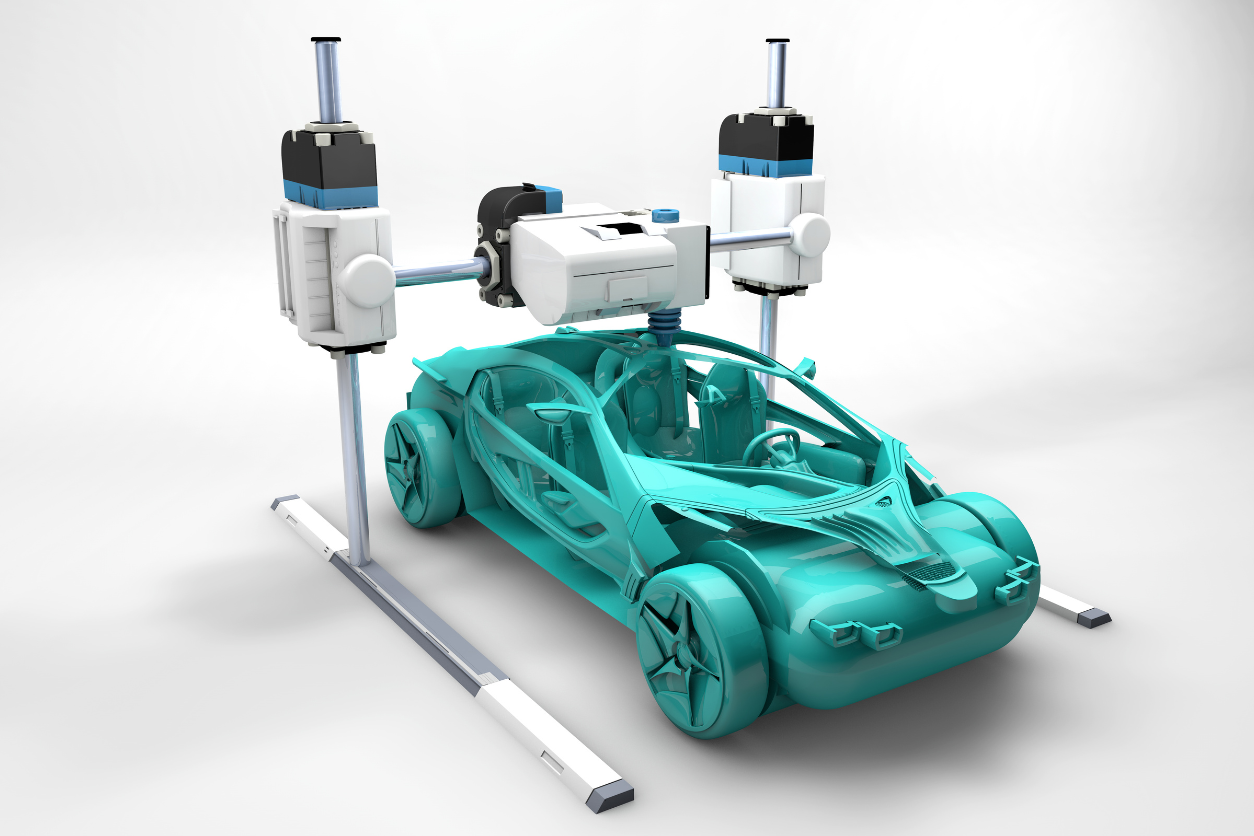
Imagine walking into a car dealership, selecting a vehicle, and having it custom-built just for you—right down to the smallest details—using advanced 3D printing technology. While this might sound like a scene from a sci-fi movie, it’s closer to reality than you might think. 3D printing, once a novelty used for creating small prototypes and hobbyist projects, is now making serious waves in the automotive industry. But is it truly a game changer, or just another flashy trend?
Let’s hit the gas and explore how 3D printing is revolutionizing car manufacturing, what it means for the future of the industry, and whether it’s a sustainable shift or just a blip on the radar.
The Nuts and Bolts of 3D Printing in Cars
First, a quick pit stop on what 3D printing actually entails. In the simplest terms, 3D printing—also known as additive manufacturing—works by building objects layer by layer from digital designs. Instead of starting with a block of material and carving away excess (like traditional manufacturing), 3D printing adds material only where it’s needed, which minimizes waste and allows for incredibly complex designs.
In the automotive world, this technology initially found its footing in rapid prototyping. Car manufacturers could quickly print out components to test for fit, function, and design—cutting down on the time and costs associated with traditional prototype development. But as the technology has advanced, it’s moved beyond just prototyping and is now being used for actual production parts.
Why It’s a Big Deal
So, why is 3D printing such a big deal for car manufacturing? There are a few reasons, and they’re not just about saving money (though that’s a big part of it).
Customization on a New Level
Traditional car manufacturing relies heavily on mass production—cranking out thousands of identical parts. 3D printing flips this script. Because each part is created from a digital file, manufacturers can easily tweak designs to create custom components without the need for new molds or tooling. This opens up a world of possibilities for personalization. Want a car interior that’s uniquely yours? 3D printing could make that happen.
Speeding Up Innovation
The automotive industry is notorious for its long development cycles. New cars take years to go from concept to showroom. 3D printing can slash these timelines by allowing manufacturers to quickly produce and test parts. This means faster iteration, quicker improvements, and ultimately, bringing innovative features to market in record time.
Sustainability
With the world increasingly focused on reducing waste, 3D printing offers a more sustainable approach to manufacturing. Because it only uses the material needed for the part, there’s significantly less waste compared to traditional manufacturing processes. Plus, many 3D printing materials are recyclable, and some companies are even experimenting with bio-based materials.
Current Real-World Examples
3D printing isn’t just a theoretical game changer—it’s already being used by major automotive players. Here’s a look at how some of the industry’s biggest names are putting 3D printing to work:
- Ford: Ford has been using 3D printing for years, not just for prototyping but also for producing parts used in manufacturing. In fact, the company has stated that 3D printing has allowed them to reduce the cost of prototype parts by up to 50%. They’re also exploring the possibility of printing parts directly onto a vehicle’s body, potentially creating lighter, more efficient designs.
- Porsche: Porsche has taken 3D printing into the world of high-performance cars. The company recently announced that it’s using 3D printing to produce lighter, stronger pistons for its 911 GT2 RS model. These pistons are not only more durable but also help improve the car’s performance by reducing its overall weight.
- Local Motors: Perhaps the most radical example comes from Local Motors, a company that 3D-printed an entire car. The Strati, which made headlines a few years ago, was printed in just 44 hours and assembled in less than a day. While the Strati is more of a concept than a car you’d see on the highway, it demonstrates the potential of 3D printing to completely rethink how cars are built.
The Road Ahead: Challenges and Opportunities
Of course, no game-changing technology comes without its challenges. One of the biggest hurdles for 3D printing in car manufacturing is scale. While it’s great for producing small batches of custom parts, scaling up to mass production is still tricky. The technology needs to become faster and more cost-effective to compete with traditional manufacturing for large-scale production.
Another challenge is material limitations. While 3D printing materials have come a long way, they still can’t match the variety and performance of materials used in traditional car manufacturing. However, ongoing research into new materials—especially high-performance composites and metals—is quickly closing this gap.
So, is 3D printing in car manufacturing a true game changer? The answer seems to be a resounding “yes,” but with a caveat. It’s not a magic bullet that will replace all traditional manufacturing methods overnight. Instead, it’s a powerful tool that’s slowly but surely integrating into the industry, offering new possibilities for innovation, customization, and sustainability.
As the technology continues to evolve, we can expect to see more 3D-printed components in our vehicles—and maybe one day, even fully 3D-printed cars. So, buckle up, because the future of car manufacturing is being printed, layer by layer, right before our eyes.